在汽车里面,由于汽车所面对的环境温度在一个很宽泛的范围,所以对于汽车内部的热管理是一个很大的课题。汽车热管理的出发点更多偏向于“各个零部件没有热害风险”,每个零部件的性能、成本和发展趋势都是不一样的。在设计中,需要从考虑恶劣工况下部件热害风险,考虑低负荷工况下,热管理系统的效率,在冷热两种工况下的能量耗散和改善热效率。本文从部件和材料的角度来探讨一下设计和材料的问题。
第一部分 智能电动汽车提出的新需求
1) 锂电池在汽车行业里面的应用
锂电池是一个重要的能源,如前面所述,在汽车里面可以分为12V电池、48V电池、HEV高压电池、PHEV电池和BEV电池。这些电池从3.6Ah逐渐上升到200Ah以上。从热管理的角度,可以分为被动散热、液冷和冷媒直冷等方式。
l 12V电池:辅助供电,电流大,需要被动散热
l 48V和HEV电池:能量回收,电流大,在设计中可以采用被动散热、风冷两种不同的形式,也有企业考虑选用液冷
l 动力电池:驱动车辆,功率输出持续性,目前主流的选择是采用主动冷却的方式进行
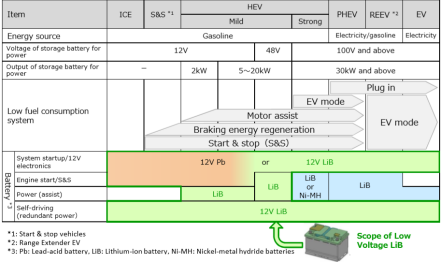
图1 锂电池在汽车里面的应用
在汽车里面,锂电池的工作温度区间是有限的,如下图所示,在低温区和高温区,温度都会影响电池的工作特性,特别是在高温区影响电池寿命,低温区工作甚至会影响安全。
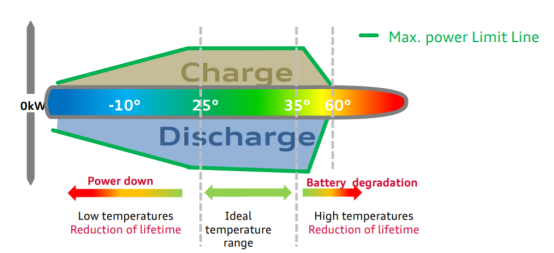
图2 锂电池的工作区域
因此电动汽车的动力锂电池组热设计是保证电池可靠工作的关键技术,而如何把电芯的热量导出来是核心的设计考量因素。通常动力电池组液冷散热部分由液冷管和导热胶组成,液冷管包括内部的冷却液,重要完成锂离子电池组工作出现热量的散热,导热胶完成电芯与液冷管之间的热传导。导热胶是目前新能源电动汽车应用较为广泛的导热材料,能够在室温条件下通过加成固化反应形成一种柔软、有弹性且表面具有粘附性的有机硅弹性体,同时还具有优异的电气绝缘性能。
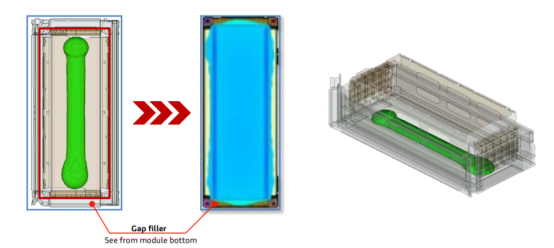
图3 导热胶的传导
2) 功率电子的使用
在为电动汽车开发高功率密度电子技术的过程中,核心的挑战是管理功率电子(逆变器DC-AC、直流变压器DCDC、充电机ACDC)在高负荷工作所产生的热量。经过实践,在这方面采用导热灌封化合物是一种快速有效地将热量从功率部件传导到散热器。对于功率电子器件来说,半导体工作温度也是有天花板的,高温区会影响寿命。
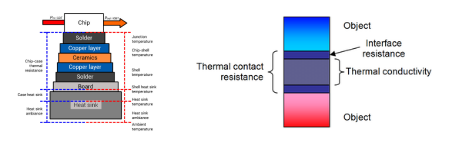
图4 功率电子方面的热传导
3)智能汽车的核心运算计算机
在车载计算平台的设计领域,为了保证自动驾驶的实时性要求,需要保证软件响应的最大延迟在可接受的范围内,对于计算资源的要求也因此变得极高。未来的计算平台是异构的,会使用CPU+GPU+FPGA的计算平台,计算所需要的功率非常大。因此在未来开始衡量算力和功耗,需要通过导热技术把热量尽快带出。

图5 未来车载电脑的计算量需求
第二部分 导热材料在这些应用中起到作用
在这种设计中,需要根据不同的需求选择良好的热管理界面材料。
1) 有哪些材料可以用?
从目前来看,主要有以下的材料可以用:
a) 有机硅是一种最通用的化学物质,它的温度范围很宽(-75°C到+200°C)可以维持本身固有的弹性。在设计中考虑阻燃、耐高温和永久弹性时候,有机硅产品是作为首选的。
b) 环氧树脂具有强度高、用途广、耐用性高、粘接度强、耐化学腐蚀与耐高温的优点。
c) 聚氨酯应用在不需要耐高温的特性,聚氨酯在低温用途中的效果最好,可保护敏感的电子器件,而且具有防水性。
事实上,这些不同的材料首先是应用在不同的领域,然后慢慢扩展到汽车上的。这里我们首先来看一下有机硅材料,这方面不得不提一下陶氏,在有机硅材料领域居于世界领先地位,为全球25,000多家客户提供7,000余种有机硅产品以及相关服务。陶氏的导热有机硅材料具有广泛的粘度、固化速度和导热系数,可满足几乎所有行业的电子产品设计中对热管理日益增长的需求。导热材料业务的增长是伴随着客户和行业一起成长的。近些年,随着智能汽车和新能源汽车的快速发展,车辆越来越依赖动力电池和电子设备实现各种功能。针对汽车动力电池和电子设备日益增长的导热需求,陶氏开发了一系列更高性能、可靠性,使用寿命和更具成本效益的导热解决方案。
陶氏有机硅的专长是70多年的技术和行业经验积累,高质量上游原材料保证下游产品的稳定和可靠性,产品线宽囊括了导热填缝剂,导热粘接剂,导热灌封胶和凝胶,导热硅脂等不同类型的导热产品。此外,陶氏有机硅部门可以针对客户的具体需求快速调整导热产品的性能如粘度、固化速度和导热系数从而开发出创新产品满足不同客户需求。
以2.0/m·kW导热填缝剂为例,以前同等导热系数的导热填缝剂往往需要2.7g/cm3的密度,现如今通过本地化的技术团队以及全球技术专家的支持,新开发的2.0/m·kW导热填缝TC-5515 LT密度大幅降低28%为1.95 g/cm3, 从而满足新能源汽车等行业轻量化的需求。此外TC-5515 LT产品目前能够满足3000小时可靠性老化测试要求,3倍于行业基本要求。
2) 材料到车上的应用
实际上,原有的汽车和零部件企业和材料企业的分工,是通过产品一级级的要求来逐步完善的,整车层面主要通过预定义要求,通过完善的测试要求和售后迭代反馈来逐步晚上要求。零部件企业,通过分解需求,一步步对要求进行完善,而材料企业则是对这些要求进行性能方面的矩阵特性评估,最后迭代的链条把一个子系统逐步完善。这是一种协作和完善的过程。
由于汽车的使用年限比较长,和质量、可靠性和寿命有关的内容,如果在后期发现会比较难处理,整体的处理成本比较高,所以这套分工协作的方法就一直广泛使用。
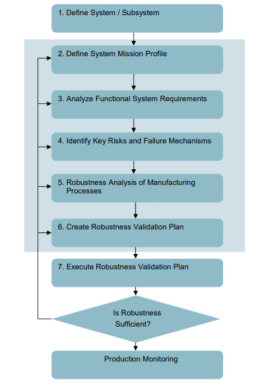
图6 逐步完善汽车的子系统
小结:随着产业界对于10年100万公里甚至是15年200万公里的电池寿命目标的提出,未来电池的热管理会扮演越来越重要的角色。